您也许对南平本地以下产品新闻也感兴趣
- 河道护栏实力老厂
- 柏莱仕BR昆明-厦门表进水气维修-中心服务维修客服
- 帕玛强尼Parmigiani漳州-三明-厦门更换表镜价格-中心服务维修客服
- DN600陆地用环氧树脂防腐钢管
- DN3000单层环氧粉末外涂层防腐钢管价格
- 真力时Zenith-龙岩-厦门换把头价格-维修-修理
- 肖邦Chopard-龙岩-厦门修理手表中心-维修-修理
- 卡地亚Cartier-莆田-厦门修理手表中心-维修-修理
- q345b钢板密度
- 45#127*20无缝管厂家电话
- 白沙县20000KVA变压器出租本地厂家信赖推荐
- 银行密集架汽轮机保温罩壳一站式供应
- 导视牌标识景观小品雕塑值得信赖
- 复合耐磨钢板耐磨钢板厂家质量过硬
- 智能密集柜性价比高的【鑫武】
当前位置:
天津 恒永兴金属材料销售
有限公司 >
南平本地每News
机械仪表用合金铝槽哪家质量好
更新时间:2024-12-25 10:55:35 浏览次数:4 公司名称:天津 恒永兴金属材料销售 有限公司
以下是:机械仪表用合金铝槽哪家质量好的产品参数
产品参数 | |
---|---|
产品价格 | 电议 |
发货期限 | 全国配送 |
供货总量 | 充足 |
运费说明 | 当天 |
品牌 | 恒永兴 |
规格 | 齐全 |
价格 | 电议 |
以下是:机械仪表用合金铝槽哪家质量好的图文视频
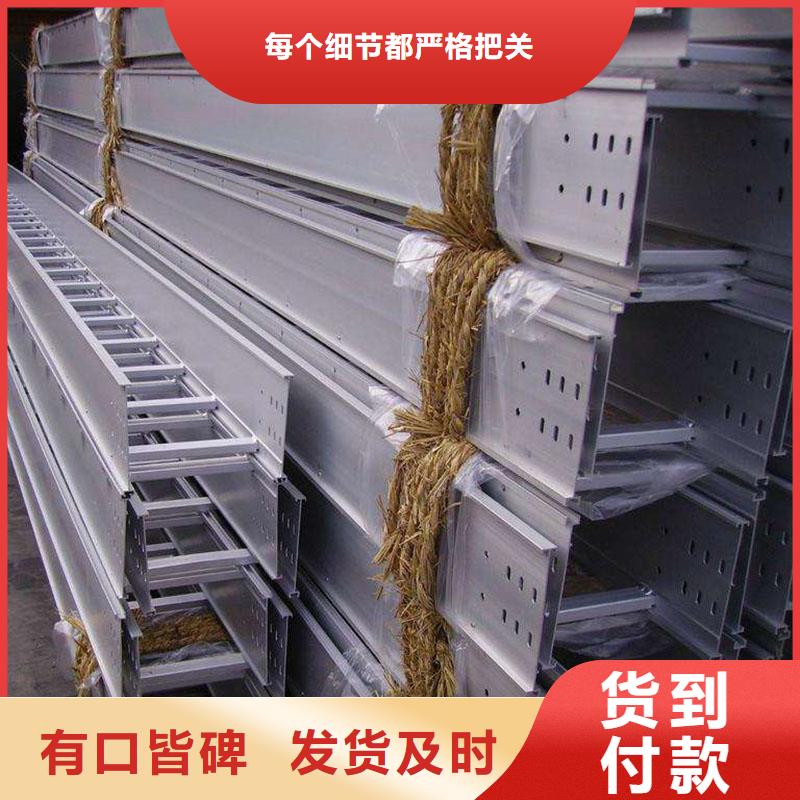

机械仪表用合金铝槽哪家质量好,恒永兴金属材料销售
有限公司为您提供机械仪表用合金铝槽哪家质量好,联系人:李经理,电话:022-86869388、18802286588,QQ:554918566,请联系恒永兴金属材料销售
有限公司,发货地:天津北辰区双街镇京津路西(北方实业发展有限公司内)发货到福建省 南平市 延平区、顺昌县、蒲城县、光泽县、松溪县、政和县、邵武市、武夷山市、建瓯市、建阳区。 福建省,南平市 南平市境域,先秦时地属百越,1994年9月,撤南平地区设地级南平市;是中国南方开发早的地区之一,境内有四千多年的历史,是福建文化的发源地之一。“福建”之名取古建州(今建瓯)首字而来。是闽越文化、朱子文化、武夷茶道文化、齐天大圣文化、张三丰太极文化的发源地。理学家朱熹在南平“琴书五十载”,影响中国800余年,谓之为“闽邦邹鲁”“道南理窟”。
想要更直观地了解机械仪表用合金铝槽哪家质量好产品吗??产品视频,带你走进产品世界
以下是:机械仪表用合金铝槽哪家质量好的图文介绍
铝板基材表面常见的四种处理--A对铝板基的技能需求:对制造PS版的铝板基较基本的技能需求是外表光滑平坦,无擦划伤、坑包、印痕、非金履压入、气孔、轧制条纹等表观缺点,厚薄一致,波涛度操控在1mm内,平直度小于2I;组 织细密均匀,无偏析、夹渣,内应力分由对称、均匀;粗糙度Ra值小于0.28,以确保电解砂目细密均匀。目前我国很多运用的板基材料为1050A、1060等。B碱洗:一般,由铝加工厂供给的铝板,其外表都带有一定量的油,油和氧化膜对砂目处置有影响,在PS版出产中常用热碱冲刷铝板进行外表处置。一般用碱液来去掉氧化膜和油。常用除油液的配比为:NaOH的质量钠等缓蚀剂及葡萄糖酸钠、脂肪酸聚氧乙烯醚类增溶、络合等外表活性剂。除油液的温度一般操控在55~60℃左右,除油的作用与溶液的温度有关。若温度太高,则造民对铝板基严重腐蚀,因此有必要操控温度。除油的时刻有必要通过仔细对比较终断定。由于,它与各种不一样出产线有关。卷筒出产线则与出产线的速度有关,以4m/min为例,除油时刻有必要这到20s,其作用才能处以确保。除油液有必要留意及时更新,由于在除油进程中会生成很多的皂化物、乳化物和铝盐,它们的存在影响除油作用,并阻止对铝板外表油污的皂化和乳化,当发现除油作用不强时,有必要及时更新。一般若通过碱泵进行循环时,除油液能坚持较长时刻,若不循环则更新时刻缩短。查看除油作用较简单的方法是用水。除油作用好的铝板外表水能均匀地附着涣散,若水倒上后,在铝板外表呈水珠状,则阐明除油作用欠好。除油的温度要常常留意,除油液的温度过低,则能够构成除油不完全。C酸洗:在出产工艺中,碱洗以后有一硝酸酸洗进程,其目的是去掉碱洗后的残留物质,中和剩余的碱液。硝酸溶液的质量浓度为5%~10%。配制时留意将硝酸小心肠倒入水中,充分混合。在酸洗进程中应常常留意溶液的浓度剖析,及时弥补。D粗化:粗化是为了构成具有需求粗糙度的砂目构造。粗化既可进步铝板基外表对水的亲和力,进步板基外表湿润量,避免版面上脏;一起粗化后的外表还可进步版同与感光剂的附着力,进而进步印版的耐印力。粗化后的砂目是由无数的凸峰和凹谷构成,不一样的砂目构造,对保水性感光层的附着力影响较大,并对PS版的运用带来较大影响。出产顶用外表粗糙度测试仪制作的砂目粗糙断面轮廓曲线的特征参数来表征。
铝基板,是原材料的一种,是一种具有良好散热功能的金属基覆铜板。它是以电子玻纤布或其它增强材料浸以树脂、单一树脂等为绝缘粘接层,一面或双面覆以铜箔并经热压而制成的一种板状材料,被称为覆铜箔层压铝基板,简称为铝基覆铜板。下面就由康电路来为大家介绍一下铝基板的性能和材料的表面处理。铝基板的性能介绍:1、优良的散热性能--铝基覆铜箔板具有优良的散热性能,这是此类板材*突出的特点。用它制成的PCB,不仅能有效地防止在其上装载的元器件及基板的工作温度上升,还能将电源功放元件,大功率元器件,大电路电源开关等元器件产生的热量迅速地散发,除此之外还因其密度小、质轻(2.7g/cm3),可防氧化,价格较便宜,因此它成为金属基覆铜板中用途*广、用量*大的一种复合板材。绝缘铝基板饱和热阻为1.10℃/W、热阻为2.8℃/W,这样大大提高了铜导线的熔断电流。2、提高机械加工的效率和质量--铝基覆铜板具有高机械强度和韧性,此点大大优于刚性树脂类覆铜板和陶瓷基板。它可以在金属基板上实现大面积的印制板的制造,特别适合在此类基板上安装重量较大的元器件。另外铝基板还具有良好的平整度,可在基板上进行敲锤、铆接等方面的组装加工或在其制成PCB上沿非布线部分折曲、扭曲等,而传统的树脂类覆铜板则不能。3、尺寸的稳定性高--对于各种覆铜板来说都存在着热膨胀(尺寸稳定性)问题,特别是板的厚度方向(Z轴)的热膨胀,使金属化孔,线路的质量受到影响。其主要原因是板材的线膨胀系数有差异,如铜的,而环氧玻纤布基板的线膨胀系数为3。两者线膨胀相差很大,易造成基板受热膨胀变化的差异,致使铜线路和金属化孔断裂或遭到破坏。而铝基板的线膨胀系数在之间,它比一般的树脂类基板小得多,而更接近于铜的线膨胀系数,这样有利于保证印制电路的质量和可靠性。铝基板材料的表面处理:去油--铝基板材表面在加工和运输过程中表面涂有油层保护,使用前必须将其清洗干净。其原理是利用汽油(一般用航空汽油)作为溶剂,可将其溶解,再用水溶性的清洗剂将油污除去。用流水冲其表面,使其表面干净,不挂水珠。脱脂-经过上述处理过的铝基材,表面尚有未除净的油脂,为了将其彻底去除,用强碱氢氧化钠在50℃浸泡5min,再用清水冲洗。碱蚀--作为基底材料的铝板表面,应具有一定的粗糙度。由于铝底材及其表面的氧化铝膜层均为两性材料,可利用酸性、碱性或复合碱性溶液体系对铝基底材料的腐蚀作用对其表面进行粗化处理。另外,粗化溶液中还需加入其他物质和助剂,使其达到下述的目的。化学抛光(浸亮)--由于铝底基材料中含有其他杂质金属,在粗化过程中易形成无机化合物粘附在基板表面,因而要对表面形成的无机化合物进行分析。根据分析结果,配制相适应的浸亮溶液,将粗化后的铝基板置于此浸亮溶液中,保证一定的时间,从而使铝板的表面干净并发亮。
说到船用铝板,大家*熟悉的要数5083铝板了。船用铝板是铝板产品研发应用的新兴领域,目前船板的生产能力已成为衡量铝板厂家综合实业的重要指标。那么,船舶制造厂家为何如此青睐5083铝板?5083铝板属于Al-Mg系合金,中等强度,具有耐蚀性好、焊接性优良、冷加工性较好的优势,广泛用于制造飞机油箱、油管、交通车辆、船舶钣金件、仪表、街灯支架、铆钉、五金制品、电器外壳等。在船舶制造领域,多采用5083H116/H321/H112状态的铝板,应用于船舶甲板、发动机台座、船侧、船底外板等部位。5083铝板满足船用铝板的选材要求:1、较高的比强度和比模量。船舶的结构强度和尺寸与材料的屈服强度和弹性模量密切相关,由于铝合金的弹性模量和密度大体相同,合金元素的添加也影响甚,因此在一定范围内提高屈服强度对减轻舰船结构有力。5083铝板属于中等强度,能同时具备优良的耐蚀性和可焊接性。2、焊接性优良。5083铝板具有良好的焊接抗裂性,在焊接时不容易出现裂纹现象。3、耐蚀性优良。耐蚀性能是船用合金的主要标志之一,5083铝板是典型的防锈铝板,耐腐性好,能适应恶劣的海洋环境,经久耐用。4、密度小。铝合金比重小,能减轻船板重量,节省能耗,增加载重。5、环保。铝合金不燃烧,遇火,而且回收利用率高,可循环再利用,环保性好。
通过温度控制提高挤压铝型材产量,通常,如果没有非预定的停机时间,那么*大产量主要决定于挤压速度,而后者受制于四个因素,其中三个固定不变而另一个则是可变的。 个因素是挤压机的挤压力,挤压力大的可在锭坯温度较低时顺利地挤压;第二个因素是模具设计,挤压时金属与模壁的摩擦通常可使通过的铝合金的温度上升35~62℃;第三个因素是被挤压合金的特性,是限制挤压速度的不可控制的因素,型材的出口温度一般不可超过540℃,否则,材料表面质量会下降,模痕明显加重,甚至出现粘铝、凹印、裂缝、撕裂等。*后一个因素是温度及其受控程度。如果铝型材挤压机的挤压力不够大,很难顺利挤压或甚至出现塞模现象而挤不动时,就可提高锭坯温度,但挤压速度应低些,以防材料的出口温度过高。每一个合金都有其特定的*优的挤压(锭坯)温度。生产实践证明,锭坯温度*好保持在430℃左右(挤压速度≥16mm/s时)。6063合金型材的出模温度不得超过500℃,6005合金的*高出口温度为512℃,6061合金的*好不大于525℃。出模温度的不大变化也会影响产品的产量与质量。挤压筒温度也是很重要的,特别应注意预热阶段的温度升高,应避免各层之间产生过大的热应力,*好是使挤压筒与衬套同时升高到工作温度。预热升温速度不得大于38℃/h。*好的预热规范是:升高到235℃,保温8h,继续升温到430℃,保温4h后,才投入工作。这样不但能保证内外温度均匀一致,而且有足够的时间一切内部热应力。当然在炉内加热挤压筒是*佳的预热方式。在挤压过程中,挤压筒温度应比锭坯温度低15~40℃。如果挤压速度过快,以致挤压筒温度上升到高于锭坯温度,就要设法使挤压筒温度下降,这不但是一件麻烦的工作,而且产量会下降。在生产速度上升过程中,有时受电偶控制的加热元件会被切断,可是挤压筒温度仍在上升。如果挤压筒温度高于470℃,挤压废品就会上升。应根据不同的合金确定理想的挤压筒温度。千万不要认为预热挤压筒是在浪费时间、消耗能源。某工厂为赶生产任务,一方面用内部电阻元件加热,另一方面又以液化气烧嘴加热。在这种情况,温度无法测量与控制,会产生巨大的热应力,内衬温度高,膨胀比外套的快,以致挤压筒裂开,并听到“炸裂”的声音。挤压轴在工作过程中会积蓄内应力,这种应力大到一定程度会产生疲劳裂纹,一旦受到非轴向的径向力作用就会断裂。因此,挤压轴的累计工作时间达到4500h后,*好进行一次应力处理,在430~480℃保温12h,然后随炉冷却到50℃以下。遗憾的是,我国很少有工厂照此处理。
生产优质表面建筑型材时,对挤压垫温度也应严格控制,以减少表面色调不一致废品量。固定挤压垫的质量比活动的好得多,能积聚更多的热量,因而能降低锭坯端头温度,能减少杂质进入型材内,有助于提高产量。美国卡斯图尔公司(Castool)采用压缩空气冷却挤压垫与挤压轴,使其温度降到50℃左右。模具温度对于获得高的产量起着重要的作用,一般不得低于430℃;另方面,也不得过高,否则,不但硬度可能下降,同时会产生氧化,主要在工作带。在模具加热过程中,应避免模具之间紧靠着,阻碍空气流通。*好采用带格的箱式加热炉,每个模放于一个单独的箱内。锭坯在挤压过程中的温度升高可达40℃左右或更高些,升高量主要决定于模具设计。为了获得*大产量,对各项温度决不可忽视,应记录各个温度并严加控制,以找出机台的*大产量与各项温度的关系。然后,铝型材挤压生产厂的员工都应牢记:温度的精密控制,对提高产量是至关重要的。
通过温度控制提高挤压铝型材产量,通常,如果没有非预定的停机时间,那么*大产量主要决定于挤压速度,而后者受制于四个因素,其中三个固定不变而另一个则是可变的。 个因素是挤压机的挤压力,挤压力大的可在锭坯温度较低时顺利地挤压;第二个因素是模具设计,挤压时金属与模壁的摩擦通常可使通过的铝合金的温度上升35~62℃;第三个因素是被挤压合金的特性,是限制挤压速度的不可控制的因素,型材的出口温度一般不可超过540℃,否则,材料表面质量会下降,模痕明显加重,甚至出现粘铝、凹印、裂缝、撕裂等。*后一个因素是温度及其受控程度。如果铝型材挤压机的挤压力不够大,很难顺利挤压或甚至出现塞模现象而挤不动时,就可提高锭坯温度,但挤压速度应低些,以防材料的出口温度过高。每一个合金都有其特定的*优的挤压(锭坯)温度。生产实践证明,锭坯温度*好保持在430℃左右(挤压速度≥16mm/s时)。6063合金型材的出模温度不得超过500℃,6005合金的*高出口温度为512℃,6061合金的*好不大于525℃。出模温度的不大变化也会影响产品的产量与质量。挤压筒温度也是很重要的,特别应注意预热阶段的温度升高,应避免各层之间产生过大的热应力,*好是使挤压筒与衬套同时升高到工作温度。预热升温速度不得大于38℃/h。*好的预热规范是:升高到235℃,保温8h,继续升温到430℃,保温4h后,才投入工作。这样不但能保证内外温度均匀一致,而且有足够的时间一切内部热应力。当然在炉内加热挤压筒是*佳的预热方式。在挤压过程中,挤压筒温度应比锭坯温度低15~40℃。如果挤压速度过快,以致挤压筒温度上升到高于锭坯温度,就要设法使挤压筒温度下降,这不但是一件麻烦的工作,而且产量会下降。在生产速度上升过程中,有时受电偶控制的加热元件会被切断,可是挤压筒温度仍在上升。如果挤压筒温度高于470℃,挤压废品就会上升。应根据不同的合金确定理想的挤压筒温度。千万不要认为预热挤压筒是在浪费时间、消耗能源。某工厂为赶生产任务,一方面用内部电阻元件加热,另一方面又以液化气烧嘴加热。在这种情况,温度无法测量与控制,会产生巨大的热应力,内衬温度高,膨胀比外套的快,以致挤压筒裂开,并听到“炸裂”的声音。挤压轴在工作过程中会积蓄内应力,这种应力大到一定程度会产生疲劳裂纹,一旦受到非轴向的径向力作用就会断裂。因此,挤压轴的累计工作时间达到4500h后,*好进行一次应力处理,在430~480℃保温12h,然后随炉冷却到50℃以下。遗憾的是,我国很少有工厂照此处理。
生产优质表面建筑型材时,对挤压垫温度也应严格控制,以减少表面色调不一致废品量。固定挤压垫的质量比活动的好得多,能积聚更多的热量,因而能降低锭坯端头温度,能减少杂质进入型材内,有助于提高产量。美国卡斯图尔公司(Castool)采用压缩空气冷却挤压垫与挤压轴,使其温度降到50℃左右。模具温度对于获得高的产量起着重要的作用,一般不得低于430℃;另方面,也不得过高,否则,不但硬度可能下降,同时会产生氧化,主要在工作带。在模具加热过程中,应避免模具之间紧靠着,阻碍空气流通。*好采用带格的箱式加热炉,每个模放于一个单独的箱内。锭坯在挤压过程中的温度升高可达40℃左右或更高些,升高量主要决定于模具设计。为了获得*大产量,对各项温度决不可忽视,应记录各个温度并严加控制,以找出机台的*大产量与各项温度的关系。然后,铝型材挤压生产厂的员工都应牢记:温度的精密控制,对提高产量是至关重要的。
恒永兴金属材料销售 有限公司始终以质量求生存、以质量求信誉、以质量求发展、以质量求效益,我们深知 福建南平不锈钢管产品质量的优劣对于一个企业的重要性,为此我们严格按照标准组织生产,从原材料进厂开始,对生产环节中各工序进行了质量跟踪把关,保证出厂的每件 福建南平不锈钢管产品合格,通过管理评审、内部质量审核,过程控制以及采取纠正与措施的自我完善机制,促进企业质量管理体系不断完善,使企业质量保证能力不断加强, 福建南平不锈钢管产品质量水平逐步提高,一年一个新台阶。
铝型材散热器生产工艺:首先贴膜不能直接贴在铬化层上,否则会影响膜的附着力;其次,贴膜后要及时喷涂不能停放时间过长,否则容易导致贴膜脱落,严重时还要重新贴膜;再次是撕膜时要控制流平时间,不能贴膜后马上撕膜,这样会对产品质量带来一定的影响;*后是两种颜色的喷涂顺序要根据具体情况确定,既要考虑到两次固化,又要考虑到遮盖效果。贴膜质量控制:散热器铝型材质量控制中贴膜质量很重要,若贴不好,会导致喷涂困难,如贴膜的张力不大、压紧程度要控制好;对形状复杂的部位要分开贴膜,贴膜后要检查贴膜是否贴牢。否则将会给喷涂带来麻烦。影响喷涂质量。公司生产的铝型材产品均由专业的技术人员严格把关,并拥有专业的生产设备,保证质量问题,客户可放心选购我厂产品。铝型材散热器的贴膜材质:首先要对贴膜材质合理选择,根据散热器铝型材产品的要求、表面处理方式,选择相应的贴膜,同是还要考虑贴膜上的胶对铝型材表面质量的影响。
缩孔是铝合金压铸件常见的内部缺陷,常出现在产品壁厚较大或者易形成热点的位置。一般来讲,只要缩孔不影响产品的使用性能,都以合格的方式来判定。然而,对于一些重要部位,如汽车发动机汽缸体的冷却水道孔或润滑油道孔,出现缩孔是不允许判定合格的。
某企业的一款铝合金制发动机曲轴箱,采用布勒28000kN冷室压铸机铸造,材质为ADC12合金,成分见表1。铸件毛坯质量为6.3 kg,后工序进行X射线探伤时发现第二个曲轴轴承孔油道出现缩孔,离油道约8 mm,存在较大的漏油风险。据统计,2017年该位置的缩孔报废率为5%,经过一系列的探索,成功地将废品率降低为0.2%。本课题从铝合金压铸件缩孔的形成机理[1-5]和铸造条件两方面出发,分析铸件产生缩孔的原因,寻求改善措施,以期为日后解决铝合金压铸件缩孔问题提供参考。一、铝合金压铸件缩孔形成机理及形态--缩孔形成机理:导致铝合金压铸件缩孔的原因较多,追溯其本源,主要是铝合金从液相向固相转变过程中铝液补缩不足而导致。常见的缩孔原因有:①模温梯度不合理,导致铝液局部收缩不一致。②铝液浇注量偏少,导致料饼薄,增压阶段补压不足。③模具存在热结或尖锐区域。④模具的内浇口宽度不够,面积较小,导致铸件过早凝固,增压阶段压力传递受阻、铝液无法补缩。⑤铸造压力设置过低,补缩效果较差。图1为铝合金铸件缩孔形成的示意图。铸件缩孔形态:缩孔是一种铝合金压铸件乃至铸件常见的内部缺陷,常出现在产品壁厚较大、模具尖角和模温温差较大等区域。图2为某款发动机曲轴箱缩孔形态,缩孔呈似椭圆状,距离轴承油道孔约10 mm,内壁粗糙,无光泽。缩孔区域铸件壁厚较大,约为22 mm;油道孔销子前端无冷却水,模温较高。汽车发动机曲轴的两大轴颈(主轴颈和连杆轴颈)工作载荷较大,磨损严重,工作时必须进行压力润滑。在此情况下,轴颈的油道孔附近若存在缩孔,将会严重影响润滑效果。二、缩孔相关对策:铝合金压铸件产生铸造缺陷的原因有产品本身的结构特征、模具设计得浇注系统及冷却系统设计不合理、工艺参数设计不合理等原因[1~4]。根据常见的铸造缺陷原因以及铝合金铸件缺陷处理流程,探索解决铝合金压铸件厚大部位缩孔的相应对策。前期分析及对策:铸件缩孔的前期分析从容易操作的工艺参数出发,通过现场测量及观察,测得模具内浇口厚度为4 mm,计算的内浇口速度为40 m/s,产品壁厚*薄处为4.6 mm;料饼厚度为25 mm;铸造压力为60MPa。由经验可知,模具设计符合产品的结构特征,模具浇注系统应该不存在增压阶段补缩不足的问题。但是,增压阶段的铝液补缩与料饼厚度和增压压力有直接的关系,合适的料饼厚度与铸造压力才能形成内部组 织致密的铸件,因此,可以怀疑缩孔是由铸造压力偏低和料饼偏薄而导致的。前期铸件缩孔的对策分为两个:①铸造压力由之前的65MPa提高至90MPa;②料饼厚度有原来的25 mm调整为30 mm。采用上述措施后,经过小批量专流验证,缩孔率由5%减低为4.8%,效果不明显,说明工艺参数不是引起铸件缩孔的主因。中期分析及对策:由于引起铸件缩孔的本质原因是铝液凝固时补缩不足而导致,而模具温度分布不均容易导致铝液凝固顺序不合理,从而补缩不足,因此,中期对策分析主要从确保合理的模具温度入手。由产品3D模型可知,铸件缩孔处壁厚为22.6mm,壁厚较大,容易引起较高的模具温度。铝液凝固时,壁厚较大铸件内部铝液由于温度较高,尚处于液相或者固液混合相,而此时内浇口进行补缩的通道可能已经凝固。这样,在增压阶段铸件无法进行铝液补缩,从而有形成缩孔的可能。为确保合适的模具温度,采用热成像仪测得脱模剂喷涂后模具*高温度为272℃(见图3),高于正常的模具喷涂后温度,其他区域模具温度及其分布整体正常。因此,需要降低缩孔处模温。另外,测得此处冷却水孔底部距离模具型腔表面距离较大为20 mm,因为较大的热传递距离会降低模具的冷却效果,所以需要对冷却水孔进行更改。为降低缩孔处模具温度,主要采取3个方法:①改善模具冷却系统。将缩孔附件的冷却水孔深度加深,由距模具表面20 mm变成12 mm,以此快速带走附近模具热量,降低模温;将所有模具冷却水管与水管统一编号,一一对应,防止模具保全时装错,影响冷却效果[5,6]。②降低浇注温度,由675℃变为645℃。③延长缩孔处模具喷涂时间,由2 s变成3 s。实施上述整改措施后,缩孔区域模具喷涂后温度大幅度降低,约为200℃,属于正常范围。缩孔率有4.8%降低到4%,说明此类措施对缩孔具有一定效果,但不能彻底解决此区域的缩孔问题。后期分析及对策:通过前面两次改善,基本保证压铸模具处于理论上的合理状态,即浇注系统设计合理、冷却系统布置合适,工艺参数设计*优。然而,铸件缩孔率仍有4%之多。铸件缩孔处壁厚为22.6 mm,远大于其他部位的壁厚,较大的壁厚可能引起铸件中心凝固时补缩不足,增压结束后此区域还没有完全凝固,继续收缩产生缩孔[7~10],模流分析见图4。因此,如何解决铸件缩孔处的补缩不足,也许才是问题的关键。一般来讲,铸件的补缩时通过料饼→浇道→内浇口→铸件这条路径进行的。由于铸件厚大部位后于内浇口凝固,切断了增压后期的补缩通道,因此无法补缩。
缩孔是铝合金压铸件常见的内部缺陷,常出现在产品壁厚较大或者易形成热点的位置。一般来讲,只要缩孔不影响产品的使用性能,都以合格的方式来判定。然而,对于一些重要部位,如汽车发动机汽缸体的冷却水道孔或润滑油道孔,出现缩孔是不允许判定合格的。
某企业的一款铝合金制发动机曲轴箱,采用布勒28000kN冷室压铸机铸造,材质为ADC12合金,成分见表1。铸件毛坯质量为6.3 kg,后工序进行X射线探伤时发现第二个曲轴轴承孔油道出现缩孔,离油道约8 mm,存在较大的漏油风险。据统计,2017年该位置的缩孔报废率为5%,经过一系列的探索,成功地将废品率降低为0.2%。本课题从铝合金压铸件缩孔的形成机理[1-5]和铸造条件两方面出发,分析铸件产生缩孔的原因,寻求改善措施,以期为日后解决铝合金压铸件缩孔问题提供参考。一、铝合金压铸件缩孔形成机理及形态--缩孔形成机理:导致铝合金压铸件缩孔的原因较多,追溯其本源,主要是铝合金从液相向固相转变过程中铝液补缩不足而导致。常见的缩孔原因有:①模温梯度不合理,导致铝液局部收缩不一致。②铝液浇注量偏少,导致料饼薄,增压阶段补压不足。③模具存在热结或尖锐区域。④模具的内浇口宽度不够,面积较小,导致铸件过早凝固,增压阶段压力传递受阻、铝液无法补缩。⑤铸造压力设置过低,补缩效果较差。图1为铝合金铸件缩孔形成的示意图。铸件缩孔形态:缩孔是一种铝合金压铸件乃至铸件常见的内部缺陷,常出现在产品壁厚较大、模具尖角和模温温差较大等区域。图2为某款发动机曲轴箱缩孔形态,缩孔呈似椭圆状,距离轴承油道孔约10 mm,内壁粗糙,无光泽。缩孔区域铸件壁厚较大,约为22 mm;油道孔销子前端无冷却水,模温较高。汽车发动机曲轴的两大轴颈(主轴颈和连杆轴颈)工作载荷较大,磨损严重,工作时必须进行压力润滑。在此情况下,轴颈的油道孔附近若存在缩孔,将会严重影响润滑效果。二、缩孔相关对策:铝合金压铸件产生铸造缺陷的原因有产品本身的结构特征、模具设计得浇注系统及冷却系统设计不合理、工艺参数设计不合理等原因[1~4]。根据常见的铸造缺陷原因以及铝合金铸件缺陷处理流程,探索解决铝合金压铸件厚大部位缩孔的相应对策。前期分析及对策:铸件缩孔的前期分析从容易操作的工艺参数出发,通过现场测量及观察,测得模具内浇口厚度为4 mm,计算的内浇口速度为40 m/s,产品壁厚*薄处为4.6 mm;料饼厚度为25 mm;铸造压力为60MPa。由经验可知,模具设计符合产品的结构特征,模具浇注系统应该不存在增压阶段补缩不足的问题。但是,增压阶段的铝液补缩与料饼厚度和增压压力有直接的关系,合适的料饼厚度与铸造压力才能形成内部组 织致密的铸件,因此,可以怀疑缩孔是由铸造压力偏低和料饼偏薄而导致的。前期铸件缩孔的对策分为两个:①铸造压力由之前的65MPa提高至90MPa;②料饼厚度有原来的25 mm调整为30 mm。采用上述措施后,经过小批量专流验证,缩孔率由5%减低为4.8%,效果不明显,说明工艺参数不是引起铸件缩孔的主因。中期分析及对策:由于引起铸件缩孔的本质原因是铝液凝固时补缩不足而导致,而模具温度分布不均容易导致铝液凝固顺序不合理,从而补缩不足,因此,中期对策分析主要从确保合理的模具温度入手。由产品3D模型可知,铸件缩孔处壁厚为22.6mm,壁厚较大,容易引起较高的模具温度。铝液凝固时,壁厚较大铸件内部铝液由于温度较高,尚处于液相或者固液混合相,而此时内浇口进行补缩的通道可能已经凝固。这样,在增压阶段铸件无法进行铝液补缩,从而有形成缩孔的可能。为确保合适的模具温度,采用热成像仪测得脱模剂喷涂后模具*高温度为272℃(见图3),高于正常的模具喷涂后温度,其他区域模具温度及其分布整体正常。因此,需要降低缩孔处模温。另外,测得此处冷却水孔底部距离模具型腔表面距离较大为20 mm,因为较大的热传递距离会降低模具的冷却效果,所以需要对冷却水孔进行更改。为降低缩孔处模具温度,主要采取3个方法:①改善模具冷却系统。将缩孔附件的冷却水孔深度加深,由距模具表面20 mm变成12 mm,以此快速带走附近模具热量,降低模温;将所有模具冷却水管与水管统一编号,一一对应,防止模具保全时装错,影响冷却效果[5,6]。②降低浇注温度,由675℃变为645℃。③延长缩孔处模具喷涂时间,由2 s变成3 s。实施上述整改措施后,缩孔区域模具喷涂后温度大幅度降低,约为200℃,属于正常范围。缩孔率有4.8%降低到4%,说明此类措施对缩孔具有一定效果,但不能彻底解决此区域的缩孔问题。后期分析及对策:通过前面两次改善,基本保证压铸模具处于理论上的合理状态,即浇注系统设计合理、冷却系统布置合适,工艺参数设计*优。然而,铸件缩孔率仍有4%之多。铸件缩孔处壁厚为22.6 mm,远大于其他部位的壁厚,较大的壁厚可能引起铸件中心凝固时补缩不足,增压结束后此区域还没有完全凝固,继续收缩产生缩孔[7~10],模流分析见图4。因此,如何解决铸件缩孔处的补缩不足,也许才是问题的关键。一般来讲,铸件的补缩时通过料饼→浇道→内浇口→铸件这条路径进行的。由于铸件厚大部位后于内浇口凝固,切断了增压后期的补缩通道,因此无法补缩。
选购机械仪表用合金铝槽哪家质量好来福建省南平市找恒永兴金属材料销售
有限公司,我们是厂家直销,产品型号齐全,确保您购买的每一件产品都符合高标准的质量要求,选择我们就是选择品质与服务的双重保障。联系人:李经理-18802286588,{QQ:554918566},地址:[北辰区双街镇京津路西(北方实业发展有限公司内)]。